Smart Locomotive Manufacturing: Material Tracking with Predix and RFID Tags
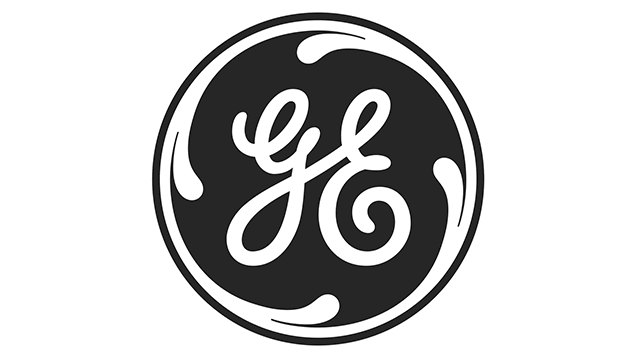
The agenda of a recent Predix meetup in Detroit was focused on IIoT solutions for coordinating supply chains in manufacturing. Ashok Madhuranath, enterprise architect and senior technologist at GE Transportation, spoke about how the Industrial Internet and real-time data can help to identify operational bottlenecks and improve legacy processes within a plant.
Why automate?
GE has more than a century-long history of serving the railroad industry, delivering freight and passenger locomotives. The newest generation of GE locomotives—the Evolution Series—was introduced in 2005. It has been upgraded since then to comply with more stringent emission standards adopted by the U.S. Environmental Protection Agency and to increase fuel efficiency.
The GE’s plant in Fort Worth manufactures more than 500 Evolution Series locomotives a year, with each locomotive comprising thousands of parts. A huge number of the materials sourced from around the world is continuously being transferred from the company’s warehouse to its 10 assembly lines.
“There’s a constant need for replenishing and making sure the parts are available where they need to be on the assembly lines.” —Ashok Madhuranath, GE
Carts are the basic units of the delivery process at Fort Worth that play a crucial role in moving parts between the warehouse and the plant. Made to carry specific materials, the carts are labeled with an identification number, order number, and destination.
Before the new tracking system was designed, the information about the carts and their location had been handled using multiple whiteboards, spreadsheets, and manual lists for cart configuration and status checks. The cart flow was lacking real-time visibility; four dedicated employees were searching for lost carts with supplies.
Developing an IoT solution with RFID and Predix
Aiming at operational and planning efficiency, the GE team implemented an RFID-based cart tracking system, pairing it with Predix capabilities for data ingestion and analytics.
At the beginning, the team identified key locations on the material workflow map and then installed RFID readers in those points. Passive RFID tags were added to more than 400 carts. (The tags have no internal power source, and a reader serves as one.)
“Our idea was to basically tag these carts with RFID tags, and in each of these specific locations, we would have an RFID reader that would identify the cart as it comes in. That data is pushed into Predix in real time.” —Ashok Madhuranath, GE
When a cart arrives at one of the scheduled points, the reader identifies it. The ClearStream RFID software running on AWS catches the reads, and the data is then ingested into Predix.
The data is pushed to Predix—where the analysis happens—every two minutes. A real-time dashboard shows where each of the carts is, as well as displays information about the parts it is carrying.
The entire tracking system was built using a microservices architecture. On the data ingestion and analytics side, the core toolset includes the Spring framework, Postgres, and Predix UI components, while Microsoft SQL Server and AWS EC2 take their part in capturing initial data. The end-user app has an AngularJS UI; among other technologies incorporated into the system design are Logstash, Kibana, and Postman.
Results and lessons learned
Since the moment the cart tracking system started to work at Fort Worth, GE has been able to:
- Achieve real-time visibility into the facility operations
- Change processes by detecting flow issues in the captured data
- Optimize resource planning based on cart locations
- Replace whiteboards and spreadsheets with a real-time dashboard and tablets
Dozens of lost carts were found at the final assembly, including those with materials.
At the end of his talk, Ashok Madhuranath shared some of the lessons learned:
- Stick with architectural simplicity.
- Design with RESTful APIs in mind.
- Split functionality into microservices.
- Go with your language of choice.
- Adopt DevOps, continuous integration, and continuous delivery practices.
- Be Agile.
It was also noted that working with reusable UI components saved the team a lot of development time.
Ashok concluded the presentation with a brief demo of the dashboard.
Want details? Watch the video!
Table of contents
|
These are the slides presented.
This video from GE sheds some light on the company’s locomotive manufacturing process.
Related reading
- Predix UI Components: Page Layout and Login
- Industrial Internet Is Powering More Efficient Well Drilling for Oil and Gas
- The Good, the Bad, and the Ugly Use of IoT: Who Owns the Data?
About the expert